Belt conveyor manufacturers prefer to use long-distance, high-capacity conveyors when designing belt conveyors. The belt conveyor is considered to be economically saved in terms of land occupation, etc. Generally, the conveying method in which the conveying line is not arranged in parallel is also adopted. In a particularly important aspect, parallel two conveyings are also used, one of which is reserved, and the belt conveyor is connected in series. . When a belt conveyor in the middle fails, the entire belt conveyor line will stop the conveying work, reducing the operating rate of the entire conveying equipment. Therefore, in order to reduce the intermediate link, a long-distance conveyor can be used to replace a plurality of short-distance conveyors.
Problems with conventional design methods for belt conveyors Conventional design methods for belt conveyors are actually a safe or conservative design approach. E.g. The selected conveyor belt safety factor and running resistance coefficient are too large, resulting in excessive motor power, wide bandwidth or high tensile strength requirements. This is not a problem for short delivery, but with the large size of the belt conveyor, these problems stand out. For example, the motor used in the design of the belt conveyor system consumes only about the actual power during operation.
When the large-scale belt conveyor is designed by conventional methods, the investment cost of the conveyor belt is too high, the tensioning device cannot be used normally, and some conveying equipment may also have local vibration problems. Optimization method of structural parameters of belt conveyor Although the structure of belt conveyor is limited by various working conditions, the working state of the conveyor is in the state of full load normal operation. After the routine design calculation method is completed, discrete variables can be used. Optimized network method to optimize the design of belt conveyor parameters.
The optimized objective function is the annual total operating cost of the belt conveyor. It includes annual depreciation maintenance fees and annual electricity bills for conveyor belts, rollers and rollers. Components such as racks, motors, and reducers have little effect on optimization results, regardless of their cost of delivery. The width, speed, strength, and idler spacing of the conveyor belt under the objective function. As well as the tension of the conveyor belt, etc., the tension of the conveyor belt can be determined by the angle of the drum working. So the objective function is the formula; the annual operating cost of the conveyor. In general, the structural parameterization of conveyor machinery is an optimization problem from the vegetable variable. The optimization method for discrete variables is not very mature. Especially for the optimization of the parameters of the belt conveying mechanism, since the constraints cannot be attributed to explicit functions and there are many constraints, for this reason, the grid method is used for optimization. The optimization method is to calculate the target by taking points in turn. The function value is compared to the best of the calculated points. If so, replace it with the current new minimum value, otherwise it will remain the same. This is done until all discrete points in the discrete design space are checked to obtain the best and best values. The outstanding advantage of the grid method is its reliability, but it will be excessively time-consuming when there are more optimization variables or more discrete values that can be taken for each discrete variable. In order to make up for this deficiency, the optimal parameters of the belt conveyor are searched in a specific way in the optimization process. In this way, the most advantageous point is at the boundary of the feasible domain or near the boundary, thus reducing the need The point of inspection.
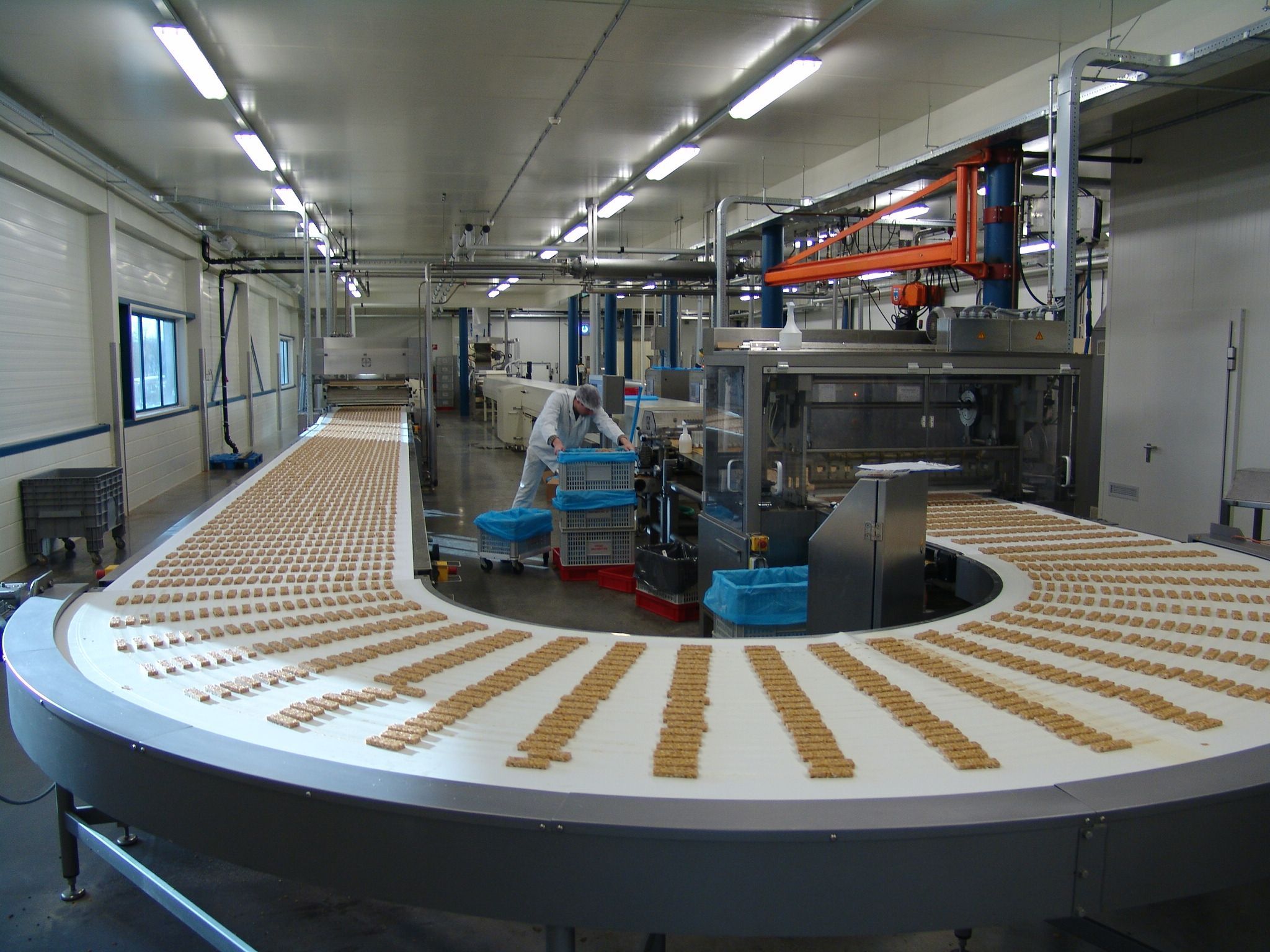